Project Brief
The aim of the project was to identify process improvements and energy saving opportunities against an existing installation which graded a food product for a national food supplier based in Scarborough, North Yorkshire. We were tasked with conducting a feasibility study on the existing feed and product transfer process to assess the existing delivery mechanism, energy consumption, and waste reduction opportunities.
Our Solution
The solution was to gather known data from the client & evaluate this against the existing process, clarifying any gaps in data. Following this we surveyed the installation of the existing process/product flume, conveying systems and vibratory conveying / grading systems detailing the existing throughput of product and evaluating the waste stream. As there were no mechanical layout drawings for the area, we created an as built 3D model, challenging where improvements could be made relating to both energy usage and minimising of waste. In doing this a revised 3D model was created removing the need for a process water flume and replacing with a conveying process which provided a 6month payback alone on reduced energy use. We then developed a design pack which included: detailed mechanical design, layout in 3D and 2D of the grading deck to incorporate a re-grade process stream to reduce waste, structural and civil modifications including a walkway design and floor repairs, electrical design and alterations of a motor control centre & software integration.
The full project scope included:
- Feasibility study.
- Scope of work.
- 2D and 3D models.
- Detailed Mechanical design.
- Structural and Civil modifications.
- Electrical design.
Project Result
We successfully provided the client with their desired information and determined how their process could be improved to reduce the overall waste. This project took 12 weeks from starting to completion and was completed in time and in full.
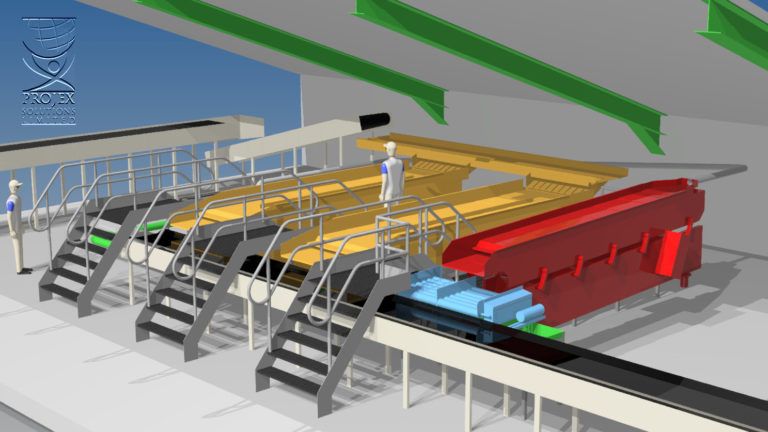