Project Brief
The aim of this project was to remove and relocate a Clean In Place (CIP) Skid system for a pharmaceutical
company in Huddersfield, West Yorkshire. The current CIP Skid system needed to be relocated so that a new Clean Room
could be built there.
Our Solution
Our solution was to determine the suitability for relocating the CIP Skid system and the strategy that was
needed to implement the system. We developed a User Requirement Specification (URS) with the client
which then led into a Functional Design Specification (FDS). We had to consider that the CIP unit needed
to be relocated to an area which was some distance away from the current location whilst causing minimal
disruption to the manufacturing area cleaning facility. We also had to create ‘As Built’ drawings as the current
drawings were dated and needed updating.
We had to check the floor loadings of the CIP Skid to ensure that they could cope with the additional
weight. We updated the CIP software and incorporated a new control panel. We proceeded to run a Factory
Acceptance Test (FAT) to ensure the new panel, existing panel and software would function correctly. The
final connections for the electrical and mechanical Installation were completed over a weekend to minimise
any further disruption to the facility.
The full project scope included:
• URS
• FDS
• FAT
• As Built Drawings
• Design
• Build
• Installation
• Commission
Project Result
In conclusion this was a successful project taking around 12 weeks from starting to completion. We had
different considerations from an engineering point of view such as the As Built Drawings and ensuring that
we followed the cGMP manufacturing guidelines. The benefits of this project were that by relocating the CIP
Skid; we provided enough space for a new clean room, the CIPD Skid was updated, and As Built Drawings
were produced.
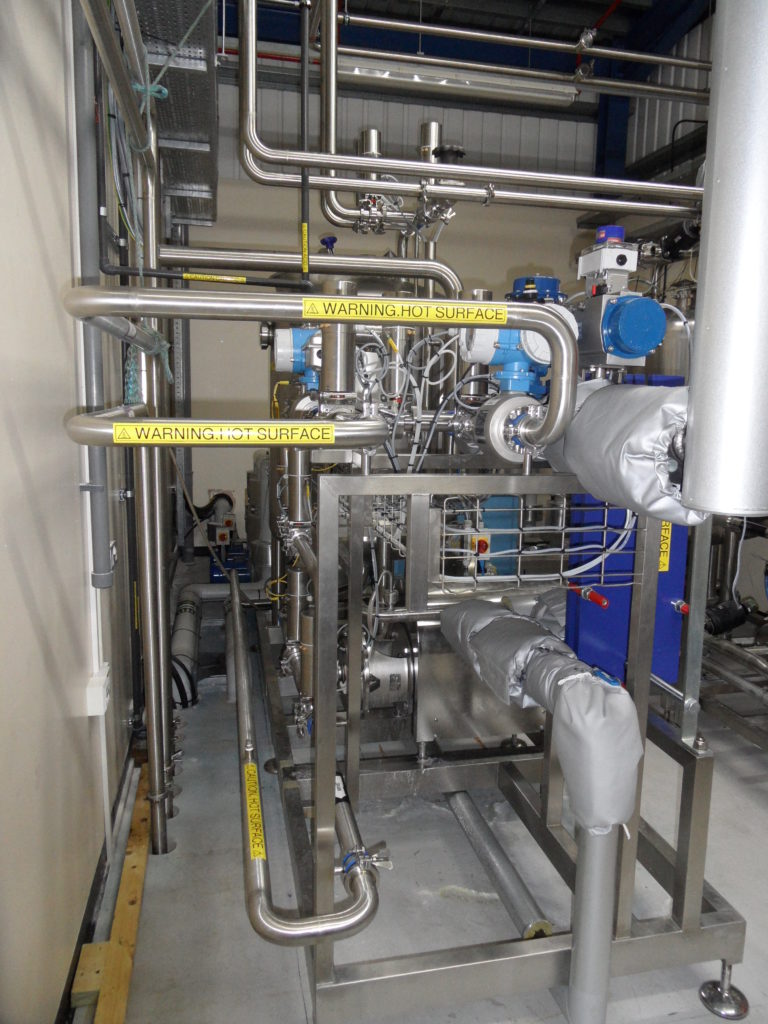
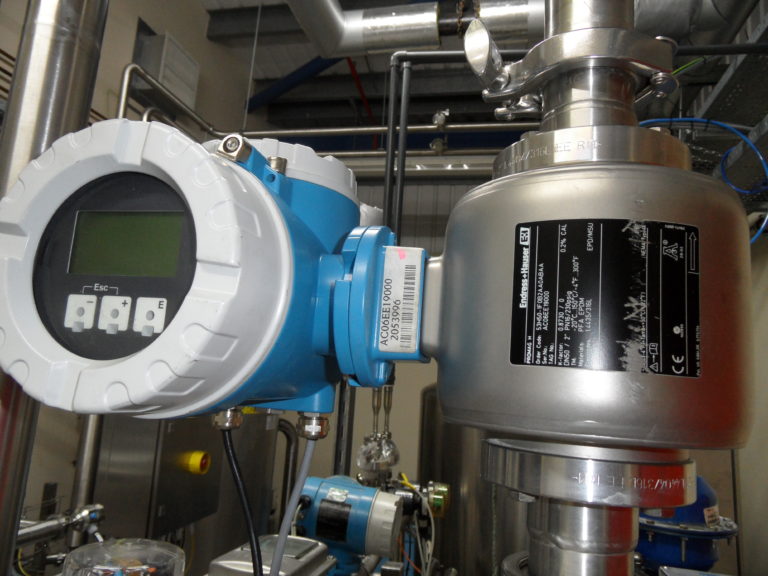
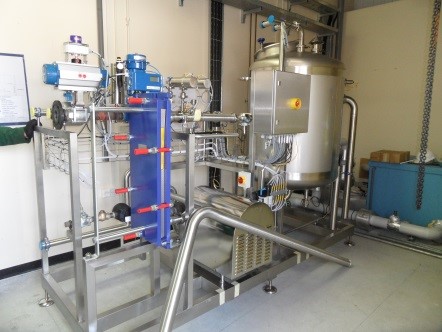